Universal Robots transform nature of manual work at manufacturing units
The company aims to manufacture easy, accessible, small and medium-sized robots to make automation available to all where people work with robots, not like robot
image for illustrative purpose
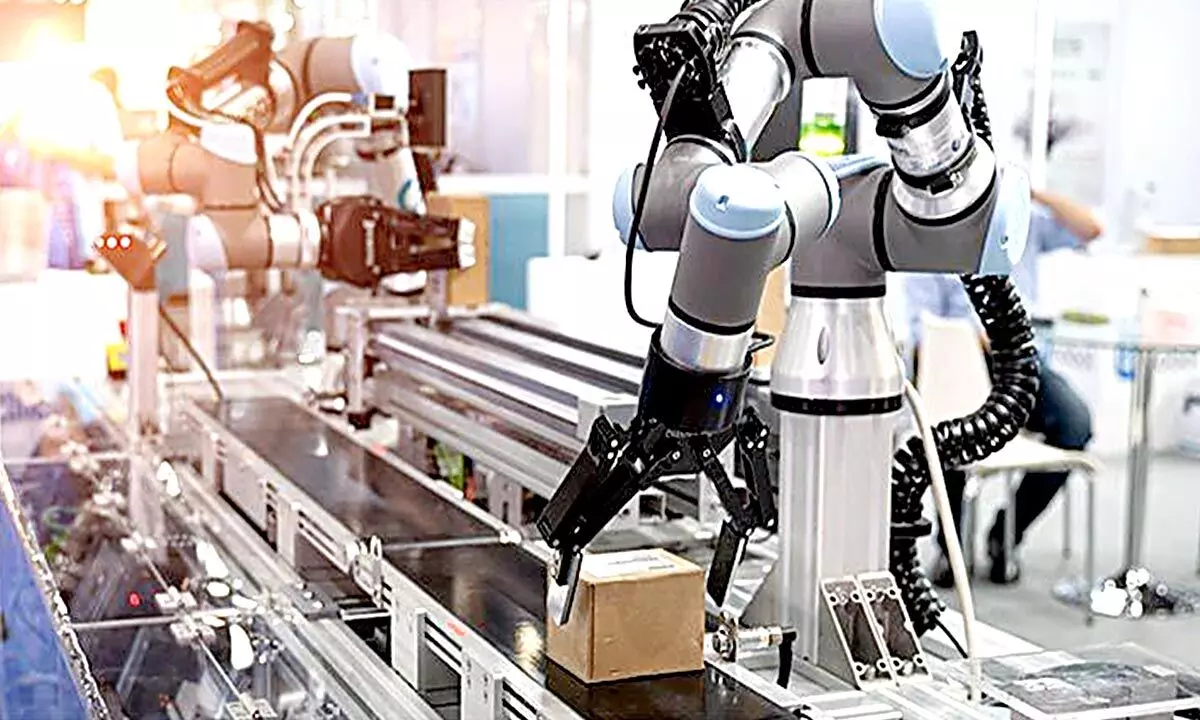
Robotics technology has changed the face of the world since its origin in 1950. The underlying focus for building such technology was to reduce the workload of humans. The first industrial robot ‘Unimate’ was made to revolutionize the manufacturing industry and since then, robotic technology has evolved manifolds. Bizz Buzz interacted with a host of industry experts to know their views.
Robotic technology has come a long way from big and bulky industrial robots to small and compact robots today. The traditional industrial robots were large and required settings like safety fences and cages. In addition, professional engineers were required to operate them on a day-to-day basis. The deployment of robots involves a huge investment; hence, only large enterprises were able to afford the robotic technology to automate their manufacturing units.
In 2005, Universal Robots came up with the vision to manufacture easy, accessible, small and medium-sized robots to make automation available to all where people work with robots, not like robots. The company wants to make robotics technology available to everyone with its simple, easy-to-use, and compact robots, which contribute to organisations being more customer-centric, resilient, and sustainable. Cobots, or collaborative robots, assist businesses in overcoming labour and skill shortages and improving employee working conditions.
Universal Robots started its journey in India with Bajaj Auto world's third-largest automotive manufacturer in the year 2010. Since then, the company has grown manifolds and has helped various brands in automating their manufacturing units and streamlining their operations such as Loreal India, Aurolab, Blue star, Dell India and many more. In addition to being useful for major businesses, Universal Robots have shown to be quite beneficial for SMEs like Shree Laxmi Agro and Shruti Engineers in attaining rapid development.
“Two-wheeler assembly lines are highly labour-intensive, spatially challenged, and have physically taxing movements requiring high-end precision. While trying to automate these lines, one of the basic requirements was standardisation. Moreover, we also wanted to be cognizant of the requirements of the large women workforce at Bajaj,” said Vikas Sawhney, General Manager of Engineering (Robotics and Automation) at Bajaj Auto.
As Bajaj rapidly expanded its production capabilities, it needed a standardised automation solution to deploy horizontally.
“Bajaj Auto chose Universal Robots primarily due to the collaborative nature of the robots. The key benefits of Universal Robots’ products, such as their compactness, low payback period, flexibility, lightweight, cost-effectiveness, accuracy, and safety, is what ultimately convinced Bajaj Auto about the suitability of Universal Robots for its standardised offerings,” Vikas added.
“We are glad to hear that Universal Robots cobots are successful in easing the assembly line processes and are very beneficial in cost reduction for Bajaj Auto. The safety measures and space-saving features are major attractive features for the deployment of cobots in Bajaj. Furthermore, our cobots are successful in bringing smiles to both Bajaj and their employees as it eases out processes for employees. In addition, cobots deliver rapid return on investment (ROI) as short as twelve months. The fast ROI is achieved through the cobot’s ability to free up employees’ time, allowing them to work on higher productivity processes,” said Sougandh KM, Country Manager for India, Universal Robots.
Universal Robots’ cobots are compact and safe to be used alongside humans. Hence, operators without robotic or programming backgrounds can operate them. The new age of technology has made the automation process faster and easier. Cobots provide a payback period as short as twelve months, making them affordable for small and medium enterprises.
The company’s robotic technology has revolutionised the way of working in the manufacturing sector. Cobots have relieved human employees from strenuous, tedious, and dangerous tasks for the labourers. Cobots have streamlined processes on the factory floor, further delivering higher production output. While countries continue to nurture young talents, the integration of cobots is attracting and retaining young engineers. As most manufacturing units are labour-force-driven, the aftermath of the pandemic has put a strain on the manufacturing units in terms of manual labour. The industry has been witnessing a huge labour shortage gap since then. Though the pandemic has left manufacturers distraught in many ways, opportunities to adopt automation and technologies have risen.
In the alarming times when everything was unsafe, safety remains at the utmost priority. Cobot technology came forward as a solution to assist manufacturers in dealing with the increased demand and fulfilling the labour shortage gap that the industry was facing. Cobots tend to operate more like humans, working at a human pace, the perfect companion for humans.
In times of social distancing, where packaged goods were preferred, cobots helped in attaining the goal of safe production where fewer humans were involved. Even today, cobots are bridging the labour shortage gap and helping industries in achieving high productivity.